Application
Roller Briquette Machines are mainly used for making powder materials into solid briquettes, like coal powders, iron dust, aluminium powder and various kind of mineral powders. These finished briquette balls can be formed as oval shape, spherical shape, oval shape, cylindrical shape, bread shape, egg shape, pillow shape, square ball shape, etc. This roller type briquette press machines are generally used in the coal industry, metallurgy industry, chemical industry, etc.
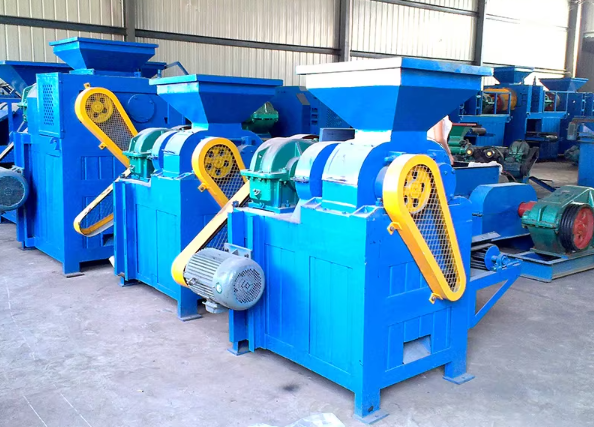
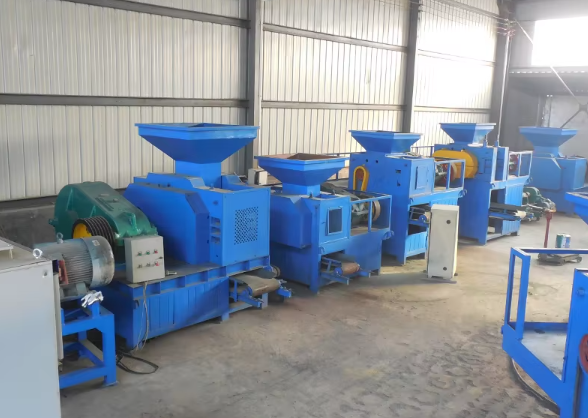
Applicable Materials
coal fines, coke fines, charcoal powder, carbon black, carbon, salt, chemical salt, iron ore fines, silicon carbide, slime, mineral powder, metal dust, cast iron dust, mill scale, manganese ore fines, fluorite powder, gypsum powder, ferrosilicon powder, and phosphor gypsum powder, nickel alloy, blast furnace ash, converter dust, coal gangue, Kaolin clay, MgO, NPK, graphite, oil shale, potash fertilizer, urea fertilizer, sea sand powder, etc.
Finished Briquettes
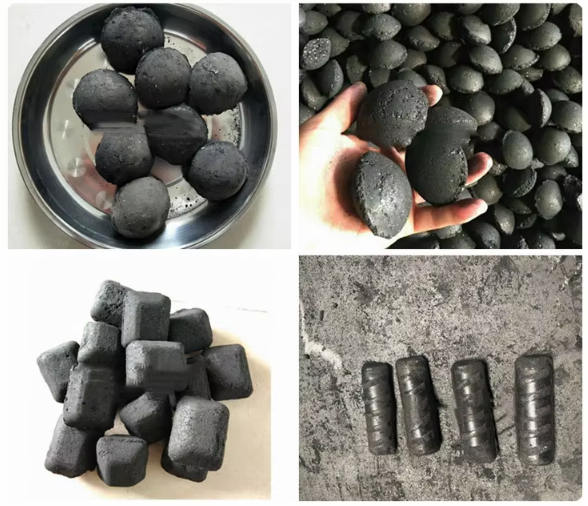
Working Principle
The electric motor gives the power to drive the driving shaft to rotate through the belt pulley and coupling. At the same time, the driven shaft also rotates against the driving shaft by the gear wheels. The rollers, which are set in the driving and driven shaftsm rotate synchronously. When the coal materials are fed into the machine and fall down to the place between the two rollers, all the coal powders will be forced into briquettes between the two squeezing rollers with the high pressure, which generates from the two rollers. While each two holes from the two rollers tough each other the pressure will reach to the peak value. As the two holes seperate and the pressure become less to zero. When the pressure come to zero, the briquettes fall down and come out of the machine.
Frame of Roller Briquette Machine
There are four main parts, one is feeding materials part;
The second is the transmission part, which includes motor, belt pulley, coupling, wheel gears and reducer;
The third is the forming part, which includes the rollers;
The forth is the discharging part.
Features of Roller Briquette Machine
- High stability, low failure rate, the finished briquettes with uniform size.
- Its pressure is higher than that of the old-version briquette machines, and its pressure can be adjustable. With this function, the briquette machine can make high-quality briquettes.
- The rollers of the briquettes are durable, and it is easy to maintain the equipment.
- Low-noise machine, and it is high-efficient and professional briquetting machine.
Rollers of Roller Briquette Machine
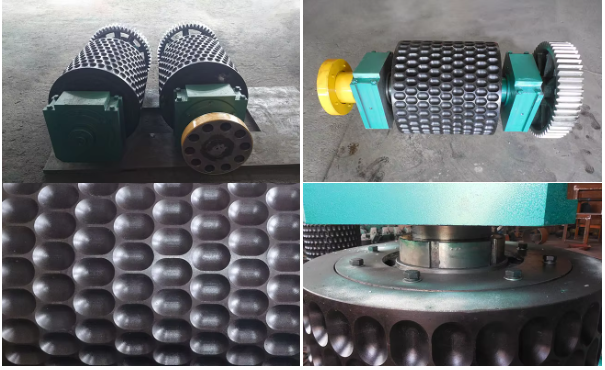
Specifications
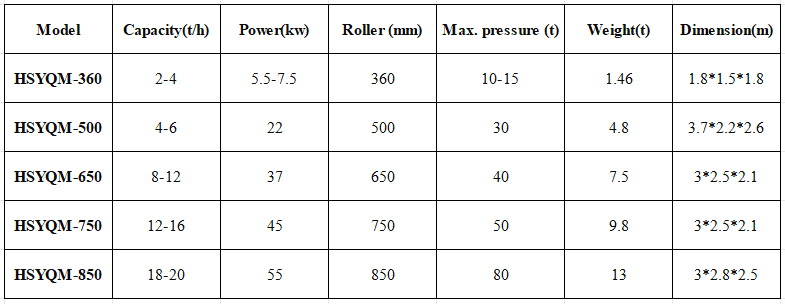
Maintenance
- Add oil for the bearings in the machine regularly every 3-7 days.
- Add lubricating oil for the gear reducer each half year. It depends on your machine situation.
- Check All the Parts Every Three Months.
Because the machine runs in the dust fly powders environment, so except the wearing parts, like rollers and bearing, so it is quite necessary for users to check the rest parts that we could not easily find and check in our daily work.
TIPS: We advise that you can take some aparts of the machine while you are checking.
Operation cautions
A. Before loading
1) Check all the screw are fully tightened or not.
2) Check all the oil is eough for gear reducer, bearings, feeder, etc or not.
3) Check the V-belt tight or not.
4) Ajust the hydraulic pressure.
5) Adjust the belt pulley and drive the rollers to move to check there is something else in the hopper and rollers.
B. During loading
1) Check and encusre no raw materials in the machine
How to start the machine? (1. main motor, 2. screw device, 3. hydraulic device, 4. feed materials)
2) Check the electricity current is normal or not.
3) Check the oil pressure is normal or not.
4) Ensure no hard materials, like iron things.
Service
- 24 Hours online technical supporting.
- We take pictures and videos for customers to know the details and production status at any time.
- For installation, we can send our drawing and engineers to customers’ place for guiding installation.
Leave a Reply