Application
Raymond mill is a high-efficiency closed-circuit pulverizing equipment for processing and grinding non-metallic minerals. The particle size of the material ground by the Raymond mill is relatively fine and uniform, and the finished product can well meet the material requirements of various fields.
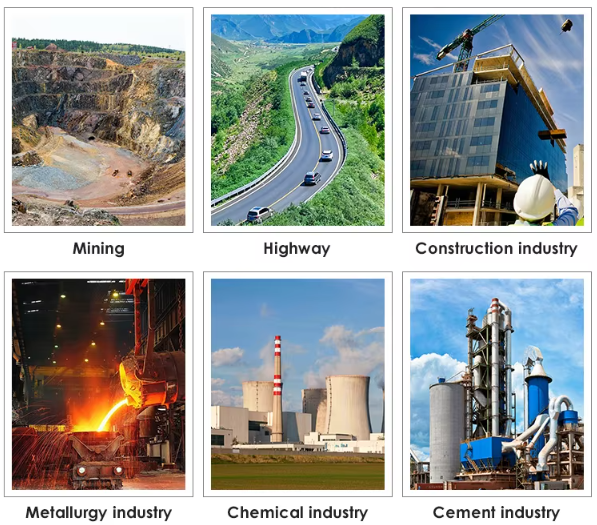
Applicable Materials
Raymond grinding mill is a super-fine ore grinding mill equipment. Suitable for processing calcite, potash feldspar, talc, marble, limestone, dolomite, fluorite, lime, activated clay, activated carbon, bentonite, kaolin, cement, fly ash, coal, phosphate rock, gypsum, glass , insulation materials and other 280 kinds of materials.
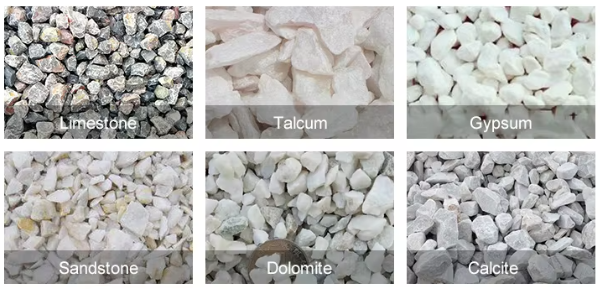
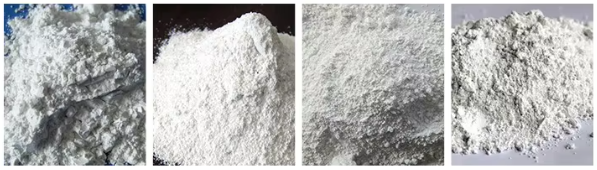
Features
1. Raymond roller mill is an efficient closed-circuit circulating powder making equipment. Compared with the ball mill, it has the advantages of high efficiency, low power consumption, small footprint, small investment and no environmental pollution.
2. Raymond grinding mill is vertical structure with small volume. From raw material rough processing to transportation to powder and final packaging, raymond mill can be an independent powder production system.
3.For Raymond mill, its application is mainly in small and medium-sized mines, chemicals, building materials, metallurgy, refractory materials, pharmaceuticals, cement, etc.
Raymond Mills in Workshop
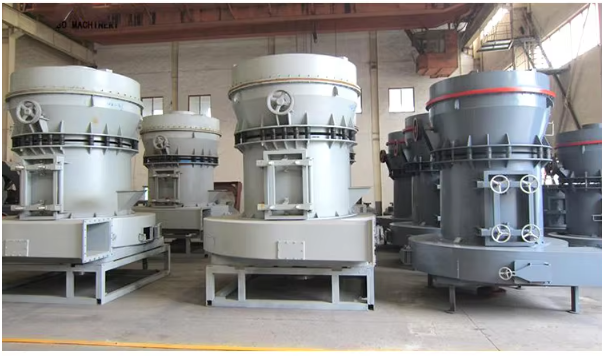
Working Principle
When the main motor power is reduced by gear reducer and the drive center axis and the plum flower frame fixed on the center shaft rotate, the grinding roll rotates around the center axis under the action of centrifugal force, and it also swings parallel around the pole shaft.
The grinding roller is made to press the grinding ring out in parallel, so that the roller and the ring are in contact with eachother. At the same time, the grinding roller revolves around the grinding roller shaft, so that the material from the shovel can be crushed and ground in the process.
The pulverized powders are sifted by the air flow of the blower to the analysis machine above the mainframe, and the coarse granularity still falls into the main engine cavity to be reground. When the finished particle size is up to the required flow into the cyclone collector, the finished product is discharged through the powder outlet tube after collection.
Raymond Mills in Workingsites
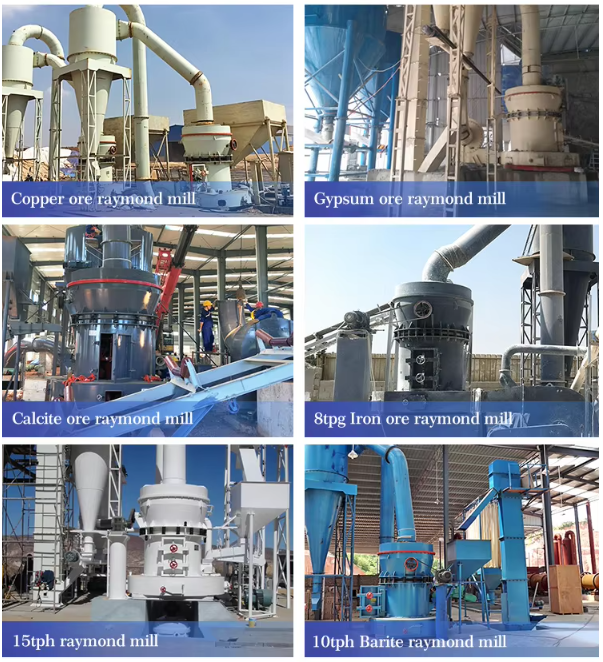
Specifications & Models
Model | Roller Size mm | Max. Input size mm | Crused Size mm | Capacity t/h | Power kw | Dimension mm |
3R1510 | 150*100 | 15 | 0.044-0.125 | 0.8-8 | 7.5 | 3250*1220*3830 |
3R2115 | 210*150 | 15 | 0.044-0.125 | 1-10 | 15 | 3520*3350*4550 |
3R2615 | 260*150 | 20 | 0.044-0.125 | 1.5-15 | 18.5 | 4650*3620*5130 |
3R2715 | 270*150 | 20 | 0.044-0.125 | 2-25 | 22 | 4750*3620*5130 |
3R3015 | 300*150 | 25 | 0.044-0.125 | 2-30 | 30 | 5360*4170*5240 |
4R3016 | 300*160 | 25 | 0.044-0.125 | 3-35 | 30 | 5450*4120*5250 |
4R3216 | 320*160 | 25 | 0.044-0.125 | 4-45 | 37 | 7120*5940*7930 |
4R3220 | 320*200 | 25 | 0.044-0.125 | 4-55 | 45 | 9950*5850*1058 |
5R4119 | 410*190 | 30 | 0.044-0.613 | 8-60 | 75 | 9220*7250*9750 |
Working Video
Leave a Reply